Handling Operations
This covers packing, processing, and distribution facilities.
Getting Started
Food Alliance certification is a voluntary means for agricultural producers and food companies to address growing customer demand for traceability, transparency, and social and environmental responsibility. This page is specifically for handling operations.
For producers interested in certification, they need to download and and review these documents:
Food Alliance Handling Operations Overview
Food Alliance Handler Certification Standards and Procedures Manual
What is the Food Alliance Handling Operations Sustainability Standard?
The Sustainability Standard describes a vision and goals for management in the following areas of concern:
Use of Food Alliance certified ingredients.
Ensure quality control and food safety.
Preserve product purity and nutritional value.
Provide safe and fair working conditions.
Conserve energy and water.
Manage solid waste responsibly.
Reduce use of toxic and hazardous materials.
Plan for continuous improvement.
It also contains the evaluation criteria used by inspectors, and lays out rules that govern the certification program.
Managers are welcome to use the criteria for self-evaluation to review practices, estimate the scores that might be received during an inspection, and identify any potential compliance issue before applying for certification.
Certification Process
Application > Site Inspection > Inspection Report > Certification
Step 1: Application
Download the Food Alliance Certified Handling Operation Application and the Food Alliance Unique Product Application.
To ensure your application is complete and reduce delays, please:
Download and complete the application forms above.
Answer all of the questions.
Sign the application documents where required.
Provide any necessary supporting documentation.
Include payment for the application fee.
This covers packing, processing, and distribution facilities.
Food handlers should review the Food Alliance Handler Certification Standards and Procedures manual before applying for certification.
Step 2: Site Inspection
Once your application is received, Food Alliance will assign a third-party auditor, who will contact you to schedule a site inspection. During the site inspection, the inspector will tour the operation and facilities, interview managers and key staff, and review relevant records to evaluate performance against the certification standards, using the handler evaluation criteria.
Step 3: Inspection Report
After the site visit, the inspector will submit an inspection report to Food Alliance.
Step 4: Certification Decision
Once the inspection report is received, it will be reviewed and the certification decision will be made. You will receive a letter specifying the decision and a copy of the site report.
Grievance Policy: If you feel that the site inspector’s findings are unfair or inaccurate, you may submit a request for re-evaluation to Food Alliance. A request must be made in writing within 30 days of receiving the official site report, detailing the perceived inaccuracies of the site inspection. Applicants should also state whether or not they would like to be inspected by a different site inspector. Re-inspections of this nature will be provided to you at no cost. No further appeals will be accepted. However, you may reapply after you have made changes to your operation as suggested in the site report.
Step 5: Maintaining Certification
Term of the Certification
The term of certification for processors and distributors is one year. The official start date will be specified in the certification letter along with the products that may be labeled as Food Alliance certified.
Ongoing Compliance and Verification
This certification is designed to provide a basis for marketplace claims of environmental and social responsibility. In order to ensure the certification criteria are being met at all times, Food Alliance reserves the right, at its own cost, to conduct unscheduled audits of participating handlers. Operations are either selected at random or based on specific concerns identified in the initial inspection.
Suspension and Revocation
If doubts are raised that an operation is not adhering to the certification standards, Food Alliance staff will investigate. If that investigation confirms the certification standards are not being met, that operation’s certification will be suspended. Food Alliance will provide the operation’s managers the reason(s) for suspension, specific steps for restoring certification, and a timeline for making the necessary changes. If the violation is remedied within the timeframe, certification will be restored. Otherwise, the certification will be revoked.
If you have any questions, or would like to receive these application forms in Word format by e-mail or a hard copy by mail, please contact our Certification Manager at (425) 466-7168 or certification@foodalliance.org.
Handling Operations FAQs
-
It is generally possible to schedule an inspection 2-3 weeks after an application is received (provided the application is complete). The certification process generally takes 6 to 8 weeks after the initial inspection. This time frame is dependent on the number and complexity of non-compliances that need to be addressed.
-
Yes. All documentation and information obtained during the certification process is held in strict confidentiality. Only Food Alliance certification program staff and site inspectors will have access to application records and documents. Food Alliance staff will not discuss applications or the details of an individual certification inspection with any individual or agency. Food Alliance site inspectors sign a binding confidentiality agreement.
-
Food Alliance certified handling operations pay both inspection fees and licensing fees annually.
Inspection Fees
Inspection Fees for handling operations include a document processing charge (which covers review of applications, coordination of the inspection, review of inspection reports, and the recommendation for certification) and the actual cost of the inspection (inspector time and travel expenses – which may vary depending upon the location, number of facilities, number of product lines, etc.).
A payment of $1,000 is due with the application, which includes the $600 document processing charge and a $400 deposit towards inspection costs. The balance for inspection costs is invoiced upon completion of the inspection and is payable in 30 days. Certification is valid for 1 year.
Handling facility inspection fees typically average between $1,500 and $4,000, but can run significantly higher.
Food Alliance can provide an estimate for inspection fees if we receive information on the facility location(s), size, product formulation, and other variables.
Licensing Fees
Licensing Fees are a percentage of sales of Food Alliance Certified products.
In many cases, the handler pays licensing fees on gross sales of certified products. However, if an ingredient supplier has already paid licensing fees to Food Alliance, the handler may subtract the cost of that ingredient and calculate their licensing fees on the net value.
(Note: A vertically integrated producer/processor would pay the inspection fee for the farm/ranch operation(s), the handler inspection fee, and licensing fees on gross sales of products that carry Food Alliance Certified content claims.)
Fees for the first year of certification are based upon actual sales, reported and invoiced at the end of each calendar quarter. Each succeeding year’s fees are based upon the most recent year’s sales of certified product.
If desired, the quarterly payment plan can be maintained after the first year.
Handler Categories
Category I – Certified Handling Operation
Includes companies that process their own product or retain other handlers to perform manufacturing or other contract services. This category also includes operations engaged in the production of ingredients intended for further processing prior to retail packaging, as well as fruit or vegetable packing and/or packaging.
Category II – Certified Handling Operation
For operations, such as brokers or distributors, that take title to product but do not change its form. Incidental re-packing for quality control or assembling orders is allowed. (Incidental repacking shall not include reducing or dividing the net weight of any previously packaged products. Incidental repacking shall also not include alteration of previously existing label information.)
Category III – Restricted Handling Operation
For handlers retained on contract to process products intended to bear Food Alliance Certified content claims. Restricted Handling Operations must pass an audit addressing baseline requirements for handling Food Alliance Certified products. However, Restricted Handling Operations are not certified and may not make claims to being certified by Food Alliance.
Licensing Fee Schedule (Annual Sales)
$0 - $500K
Category I Handler: 0.40%
Category II Handler: 0.20%
Category III Handler: 0%$500K – $2M
Category I Handler: 0.20%
Category II Handler: 0.20%
Category III Handler: 0%$2M – $50M
Category I Handler: 0.04%
Category II Handler: 0.04%
Category III Handler: 0%$50M – $100M
Category I Handler: 0.02%
Category II Handler: 0.02%
Category III Handler: 0%$100M +
Category I Handler: 0.002% or $200 minimum
Category II Handler: 0.002% or $200 minimum
Category III Handler: 0% -
Yes. We ask that all handling facility managers and decision makers be present at the time of the site inspection. In addition, we recommend the following to prepare for a site visit:
Make sure that you have ample time for the inspection. It is important that manager(s) are present as well as the person(s) responsible for record keeping and any specific areas of expertise/responsibility pertinent to your inspection and operation (see previous discussion). Site inspections typically take from four to eight hours, depending on the size of the facility and the number of products for which you are seeking certification.
Have records ready to show site inspector. This includes USDA, FDA, and HACCP & CGMP inspection records, production logs & batch records, other tracking documentation, and records of facility pesticide applications.
Be prepared to describe your system of product segregation and storage. Shipments of Food Alliance Certified product must be traceable by unique lot/batch number or receiving records to the producer or handler. Internal records must demonstrate the effectiveness of your segregation systems. Sales and shipping records must indicate the unique lot/batch numbers of Food Alliance Certified finished products or ingredients.
Be prepared to walk the inspector through your handling facility.
-
Food Alliance often contracts with independent consultants to create standards. The practices and concepts found in the standards generally come from “best management practices” identified through research at public agencies and land grant universities. The development of standards is also subject to stakeholder review, which includes farmers, ranchers and other representatives of the food industry, university and agency researchers, as well as advocates for farm labor, animal welfare, the environment and consumer affairs.
-
If an operation doesn’t meet the criteria for certification, Food Alliance will allow a fixed period to address compliance issues. The period may vary depending on the complexity of those issues. The applicant will be provided with a detailed report describing changes that would be required to meet Food Alliance’s certification criteria. When the changes are made, the applicant can contact Food Alliance to schedule another inspection. If changes are made and re-inspection requested within the fixed period, no additional fees will be incurred.
-
Yes. Please see Food Alliance’s Labeling and Marketing Guide for options to make both product and ingredient claims with less than 100% certified content.
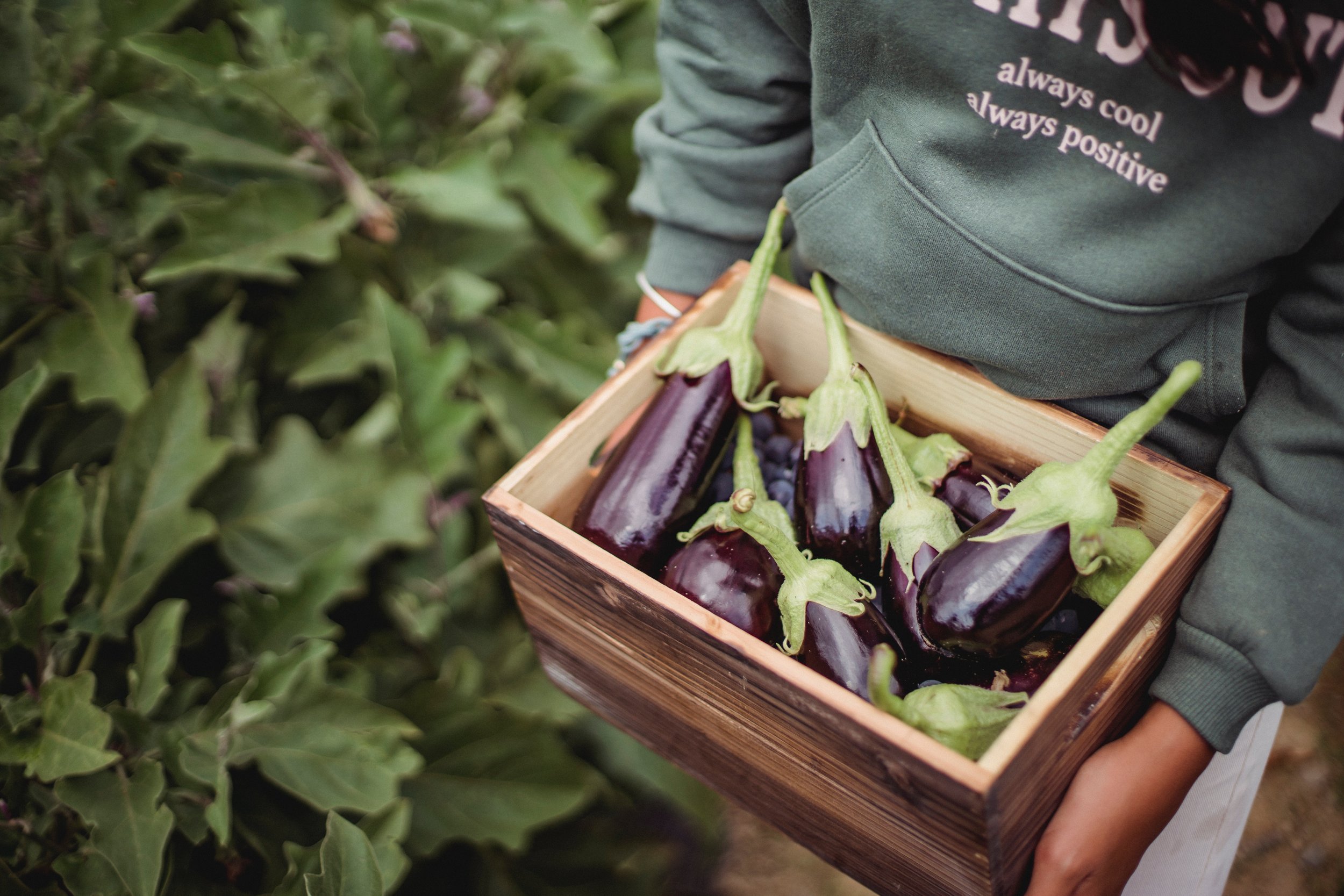